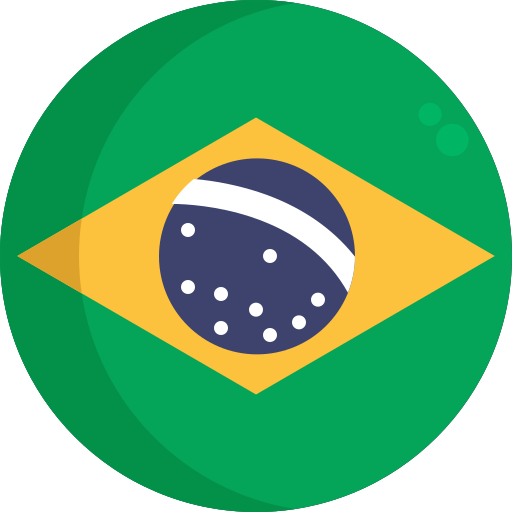
Mathematical Tools and Approaches for Polymerization Reaction Engineering
2014; Wiley; Volume: 8; Issue: 4 Linguagem: Inglês
10.1002/mren.201300198
ISSN1862-8338
Autores Tópico(s)Process Optimization and Integration
ResumoI was simultaneously honoured and delighted when Dr. Spiegel invited me to help him with the organization of this Special Issue of Macromolecular Reaction Engineering, dedicated to “Mathematical Tools and Approaches for Polymerization Reaction Engineering”. I was honoured because this particular topic is of fundamental importance for the development of polymer reaction technology, which explains the relatively large number of brilliant researchers that have worked in this field through the years. As a matter of fact, the tradition in this area dates back to the beginning of the twentieth century, when fundamental and influential modeling and numerical approaches were developed by W.H. Carothers (especially for condensation reactions), Nobel laureate J. P. Flory (especially for understanding of chain size distributions and polymer solutions) and W. D. J. Harkins, W. V. Smith and R. H. Ewart (for the complex emulsion polymerization problem).1, 2 It can be said then that technicians, engineers, and scientists understood very early and very clearly that significant developments could only be achieved in this field with the support of well-founded mathematical models and approaches. As the twentieth century evolved, it became obvious that modeling and numerical tools were also of fundamental importance for proper interpretation of available experimental data, taking into account the challenges related to the characterization of all sorts of distributions that must be used to describe the properties and performances of the final polymer products, including molecular weights, copolymer compositions, particle sizes, chain branching, block sizes, among other less frequent distributions.3-5 For this reason, it is not exactly surprising to find out that mathematical modeling and numerical tools are nowadays needed and widely used for the implementation of advanced monitoring and control schemes in both polymer laboratories and real industrial sites.6, 7 Therefore, it is no exaggeration to state that mathematical approaches constitute the realm of the polymer engineering field. I was also delighted with the opportunity because this is a particularly rich and interesting period for those who work in this area. The very fast evolution of computer resources has made possible the implementation of very detailed mathematical models and very intricate numerical procedures, also allowing for the detailed calculation of aspects of the reaction environment and of the evolving macromolecular structure that could not be imagined few years ago. As a consequence, whenever one touches this particular subject, new applications and possibilities are revealed, encouraging the continuation and the deeper investigation of old and newly found applications and possibilities. For this reason, it was certainly a privilege to be the first reader of the present issue of Macromolecular Reaction Engineering. The papers published here discuss the use of modeling and numerical tools in polymerization processes for different purposes and based on distinct techniques. The paper by Fortunatti et al.8 concerns the use of mathematical models for design of operation policies in a tubular reaction process. The use of mathematical models for design and optimization of polymerization processes constitutes a classical and important illustration of how useful numerical tools can be in this field. Special attention is given to design and control of molecular weight and copolymer composition distributions, which require refined and involving modeling of the process behavior. Particularly, the paper by Soares9 shows how instantaneous distributions can be used to model the final microstructures of the obtained polymer products. Examples include modeling of chain length distributions, copolymer composition distributions and long chain branching distributions. The papers by Aguiar et al.,10, 11 Lee et al.,12 and Calvo et al.13 discuss the interpretation of experimental data and the estimation of kinetic parameters for complex polymerization reaction mechanisms. Kinetic parameters are needed for model-based reactor design and cannot be estimated appropriately without support of sound mechanistic models. This is particularly true when nonlinear reaction steps that lead to chain branching and crosslinking are present in the reaction scheme. These papers show very clearly that the proper implementation of available numerical procedures can allow for appropriate description of the underlying complex nonlinear mechanisms. The paper by Limón and Tlacuahuac14 describes how a polymerization process model can be combined with process and operation constraints in order to allow for the on-line optimal solution of the associated scheduling and control problems. The use of complex process models for accomplishment of scheduling and control tasks on-line and in real time is becoming more important each day. On the other hand, the paper by Toledo and Tlacuahuac15 concerns the use of process models for optimization of process performance when conflicting objectives are pursued. It is important to observe that conflicting objectives are pursued in most polymerization processes, which may require the frequent use of the multiobjective problem formulation for proper design of the process operation. The paper by Poubel et al.16 regards the use of CFD (Computational Fluid Dynamics) models for computation of temperature and concentration gradients in polymerization vessels. As CFD models allow for detailed computation of the most important reactor variables as functions of time and reactor position, the number of CFD applications has grown steadily in the field, allowing for critical evaluation of well-established modeling approaches and reactor operation policies. The paper by Pladis et al.17 proposes a multi-zone modeling approach for a multi-phase reaction process that resembles the CFD approach in many aspects, including the spatial distribution of reaction variables inside the analyzed reaction vessels. I hope the readers will sincerely appreciate this very fine collection of modeling and numerical papers and will feel stimulated to (continue to) work in this very interesting and important engineering field. However, as a guest editor I must admit that there is an important gap in the present issue – the use of stochastic tools for modeling and interpretation of polymerization data. Based on this confession, we are now planning the publication of a second special modeling and numerical issue of Macromolecular Reaction Engineering, dedicated exclusively to stochastic modeling and numerical approaches for polymerization problems. See you there. Zé Carlos José Carlos Pinto obtained his BSc in Chemical Engineering at Universidade Federal da Bahia (Salvador, Bahia, Brasil) in 1985, his MSc in Chemical Engineering at Universidade Federal do Rio de Janeiro (Rio de Janeiro, Rio de Janeiro, Brasil) in 1987 and his DSc in Chemical Engineering at Universidade Federal do Rio de Janeiro in 1991. At present he holds a position of Professor Titular at Programa de Engenharia Química/COPPE, Universidade Federal do Rio de Janeiro, is Professor Permanente at Programa de Pós-Graduação em Química, Instituto Militar de Engenharia, and is a full-member of the Academia Brasileira de Ciências. José Carlos has worked in the general field of modeling, simulation, and control of polymerization processes since 1987.
Referência(s)