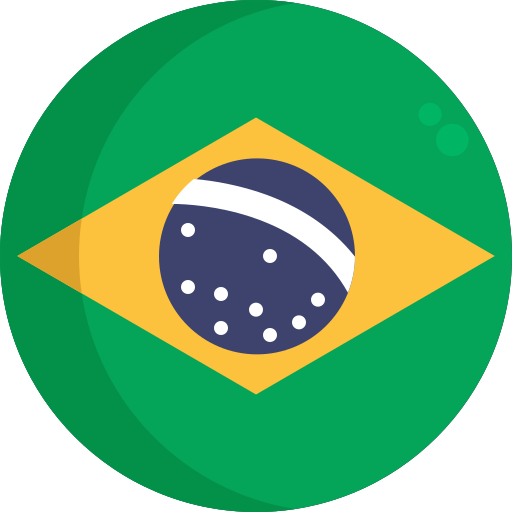
Conception of an electric propulsion system for a 9 kW electric tractor suitable for family farming
2019; Institution of Engineering and Technology; Volume: 13; Issue: 12 Linguagem: Inglês
10.1049/iet-epa.2019.0353
ISSN1751-8679
AutoresRodnei Regis de Melo, Fernando Luiz Marcelo Antunes, Sérgio Daher, Hans Heinrich Vogt, Daniel Albiero, Fernando Lessa Tofoli,
Tópico(s)Electric Vehicles and Infrastructure
ResumoIET Electric Power ApplicationsVolume 13, Issue 12 p. 1993-2004 Research ArticleFree Access Conception of an electric propulsion system for a 9 kW electric tractor suitable for family farming Rodnei R. Melo, Corresponding Author Rodnei R. Melo rodnei.melo@ifce.edu.br Department of Electrical Engineering, Federal University of Ceará, Fortaleza, 60455-760 Ceará, BrazilSearch for more papers by this authorFernando L.M. Antunes, Fernando L.M. Antunes Department of Electrical Engineering, Federal University of Ceará, Fortaleza, 60455-760 Ceará, BrazilSearch for more papers by this authorSérgio Daher, Sérgio Daher Department of Electrical Engineering, Federal University of Ceará, Fortaleza, 60455-760 Ceará, BrazilSearch for more papers by this authorHans H. Vogt, Hans H. Vogt Department of Electrical Engineering, Federal University of Ceará, Fortaleza, 60455-760 Ceará, BrazilSearch for more papers by this authorDaniel Albiero, Daniel Albiero Faculty of Agricultural Engineering, Campinas State University – UNICAMP, Campinas, 13083-875 São Paulo, BrazilSearch for more papers by this authorFernando L. Tofoli, Fernando L. Tofoli orcid.org/0000-0001-7313-9060 Department of Electrical Engineering, Federal University of São João del-Rei, São João del-Rei, 36307-352 Minas Gerais, BrazilSearch for more papers by this author Rodnei R. Melo, Corresponding Author Rodnei R. Melo rodnei.melo@ifce.edu.br Department of Electrical Engineering, Federal University of Ceará, Fortaleza, 60455-760 Ceará, BrazilSearch for more papers by this authorFernando L.M. Antunes, Fernando L.M. Antunes Department of Electrical Engineering, Federal University of Ceará, Fortaleza, 60455-760 Ceará, BrazilSearch for more papers by this authorSérgio Daher, Sérgio Daher Department of Electrical Engineering, Federal University of Ceará, Fortaleza, 60455-760 Ceará, BrazilSearch for more papers by this authorHans H. Vogt, Hans H. Vogt Department of Electrical Engineering, Federal University of Ceará, Fortaleza, 60455-760 Ceará, BrazilSearch for more papers by this authorDaniel Albiero, Daniel Albiero Faculty of Agricultural Engineering, Campinas State University – UNICAMP, Campinas, 13083-875 São Paulo, BrazilSearch for more papers by this authorFernando L. Tofoli, Fernando L. Tofoli orcid.org/0000-0001-7313-9060 Department of Electrical Engineering, Federal University of São João del-Rei, São João del-Rei, 36307-352 Minas Gerais, BrazilSearch for more papers by this author First published: 06 November 2019 https://doi.org/10.1049/iet-epa.2019.0353Citations: 20AboutSectionsPDF ToolsRequest permissionExport citationAdd to favoritesTrack citation ShareShare Give accessShare full text accessShare full-text accessPlease review our Terms and Conditions of Use and check box below to share full-text version of article.I have read and accept the Wiley Online Library Terms and Conditions of UseShareable LinkUse the link below to share a full-text version of this article with your friends and colleagues. Learn more.Copy URL Share a linkShare onFacebookTwitterLinkedInRedditWechat Abstract This study presents an updated review of the application of electric tractors. A customised drive system for the conception of a novel low-power electric tractor suitable for family farms is also introduced and discussed. The introduced system comprises several aspects regarding energy generation, transmission, conversion, storage, utilisation, conservation, and management, as well as sustainability issues. A 9 kW prototype composed of two three-phase induction motors, two independent inverters, and a lead–acid battery bank is presented. Flexible and safe operation is ensured by using an electronic control unit specifically designed for this project, as a dedicated control algorithm is also developed to provide greater versatility under common rural activities. Also, a supervisory system is proposed for data storage and performance analysis. To verify the proper performance of the electric tractor, the methodology used for conducting drawbar tests has been based on document CODE 2 by Organisation for Economic Co-operation and Development (OECD). Experimental results are presented and discussed; thus, demonstrating that the proposed electric tractor is technically feasible in terms of performance when compared with a similar internal combustion engine one. 1 Introduction Family farming stands out as one of the fastest-growing segments of food production, being of great importance to food security in many places around the world. It has also been a great ally to sustainability and socio-environmental responsibility [1, 2]. Family farms represent most of the farm systems globally, whose sizes vary from 1 to 10,000 ha [3]. In Brazil, the average size of family farms is estimated at 18 ha. It is also worth mentioning that smallholder agriculture is a complementary activity to large-scale farming, being extremely important in developing countries, where it leads to the creation of jobs in rural areas and increase of families’ income [3]. Large farms typically have abundant resources available to invest in equipment, novel technologies, and employees to increase productivity. However, this is not the case of small farms, which should rely on effective government policies for this purpose. In this scenario, the appropriate agricultural mechanisation is an imminent necessity [4]. Tractors have been one of the most important tools associated with modern agriculture. Considering the need to further reduce the greenhouse gas emissions and the eventual scarce availability of fossil fuels shortly, electric tractors have been proposed by many manufacturers as a possible solution in the context of more sustainable farming [5]. However, most commercial equipment consists of high-power machines, which are only feasible to large-size properties. In fact, low-power tractors based on electric propulsion systems are not easily found either in the market or even in the literature, being this a prominent research topic that can contribute significantly to the development of family farming [6]. The development of power trains for urban electric vehicle (EVs) has been the focus of many works available in the literature. For instance, an analytical model comprising of the electrical and mechanical systems of an EV is proposed in [7]. The powertrain is composed of a battery pack, an energy management system, a direct current (DC)–DC converter, a DC–AC inverter, and permanent-magnet synchronous motor associated with a control system, as well as power transmissions, axial shaft, and wheels. The performance is thoroughly investigated and compared with that of a conventional internal combustion engine (ICE) vehicle in terms of carbon dioxide emissions while considering distinct scenarios for the generation of electricity; thus, showing that this is the prominent solution for the increase of energy efficiency. A methodology for the modelling and design of an electric powertrain considering electromagnetic, mechanical, and thermal aspects of the required components is introduced in [8], but the conclusions are only supported by theoretical remarks and not results obtained in field tests. An energy management strategy for a dual motor-driven electric powertrain is also investigated in [9], where it is effectively demonstrated that the driving cycle influences the performance, design, and control of EV powertrains directly. Once again, experimental results are not presented and discussed. Although there are several studies dedicated to the analysis of urban EVs, only a few works are effectively focused on the performance analysis of electric tractors. A review on the state-of-the-art of electric propulsion systems applied to tractors and agricultural machinery is presented in [10]. It is evidenced that the use of electric machine drives leads to increased energy efficiency while also bringing versatility to rural activities. The authors also mention that the Agricultural Industry Electronics Foundation developed the ISO11783 (ISObus) standard in 2002 to promote compatible communications between the tractor and implements of any manufacturer. The application of EVs in rural areas is also described in [11]. According to Magalhães et al., few patents related to agricultural tractors employing electric propulsion systems were requested over the last 30 years. Even though there is a growing concern to find alternatives to replace conventional ICE tractors with electric counterparts, this aspect is still incipient; thus, justifying the need for additional research effort in this field. Besides, among the prototypes described in Table 1, there is no design approach focused on a propulsion system based on the use of two three-phase induction motors operated by an electronic control unit (ECU) and two low-power inverter drives, being this configuration more compatible with the development of family farming activities. Table 1. Brief summary of electric tractor designs Authors Traction motors Motor type Power, kW Rodrigues et al. [12] 1 AC induction motor or DC motor 2.2 Chen et al. [13] 1 BLDC motor 7.5 Gay et al. [14] 1 AC induction motor 10 Escorts Group [15] 1 AC induction motor 19 Seo et al. [16] 1 permanent-magnet synchronous motor 20 FENDT [17] 1 — 50 New Holland [18] 1 — 100 Liu et al. [19] 1 BLDC motor 130 John Deere [20] 1 — 150 The work in [21] addresses the operational feasibility of agricultural tractors powered by electricity. The performed study is based on the development of a small-scale prototype of EVs rated at 40 W using a DC motor. Besides, the introduction of a theoretical configuration for the electric tractor using a single electric motor is analysed. However, a detailed analysis of the motor drive and control system associated with the electric tractor is not presented, as well as the performance evaluation of a real scale prototype. On the other hand, the performance of a micro-tractor is investigated in [12] using three different types of motors: a three-phase alternating current (AC) motor rated at 2.2 kW, 220 Vac, and 3465 rpm; a DC motor rated at 2.2 kW, 36 Vdc, and 2900 rpm; and an ICE rated at 2.6 kW and 3600 rpm. The driving performance of an electric tractor is assessed in [1], where a single 10 kW three-phase AC electric motor is used to replace 10 kW ICE in an experimental prototype. Similarly, a 20 kW permanent-magnet synchronous motor is employed in the design for an electric tractor in [16] based on the output characteristics of a conventional tractor. However, the analysis is limited to the design of the engine and experimental results with the effective application of the motor to drive a tractor are not presented to demonstrate the claimed advantages. A control system approach for a medium-power hybrid electric tractor based on a controller area network (CAN) bus is introduced in [22], where the study is essentially focused on hardware and software developments. Several ECUs are employed, each one of them for a specific subsystem connected to a CAN bus. A drive control system for an electric tractor prototype using a brushless DC motor (BLDC) with a nominal voltage of 72 V and a rated power of 7.5 kW is proposed in [13]. The dual-loop proportional–integral–derivative control comprising of an external speed control loop and internal current loop combined with pulse-width modulation control is adopted as the motor drive control strategy. The motor controller is designed based on field programmable gate array (FPGA), where the hardware consists of NI myRIO used as the control core while integrating ARM® to the Xilinx FPGA. LabVIEW is used as the development environment for the control system. Another research found in the recent literature is the design of a load torque control strategy to improve the energy conversion efficiency of the 130 kW BLDC motor for an electric tractor, which can be pure electric or hybrid as described in [19]. The study comprises of mathematical modelling and performance analysis using simulation. The possibility to integrate renewable energy sources associated with the use of electric tractors in family farming activities is suggested in [6]. Considering that the electric tractor is supposed to operate during 15 h/day and a total of 1000 h/year on average, the energy surplus that is not eventually extracted from the battery bank can be used in applications or even injected into the grid. It is also worth mentioning that the study carried out in [6] is limited to a theoretical analysis. It is reasonable to state that major challenges for the popularisation of electric tractors include the development of novel control strategies to improve driving flexibility, manoeuvrability, and energy management, as well as the evolution of technology associated with electric machine drives, power electronic converters, and energy storage devices, while also taking into account the minimisation of cost. Within this context, this work aims to propose a customised drive system for the conception of a 9 kW electric tractor with two independent traction wheels, being compatible with family farming. The remainder of this work is organised as follows: Section 2 presents the proposed 9 kW electric tractor. Section 3 describes the experimental results of tests carried out with the electric tractor. Finally, the conclusive remarks are given in Section 4. 2 Proposed 9 kW electric tractor From the literature review, it was found that research related to propulsion systems applied to electric tractors and the respective performance analyses are not well-discussed in the existing works. A propulsion system with two independent traction wheels and a dedicated ECU specially designed for a small-sized electric tractor have not yet been developed considering the existing approaches summarised in Table 1. In this context, it is evident that there are few propositions that specifically meet the needs of small farmers in terms of small and low-power electric tractors, being this a literature gap that must be properly explored. According to a research developed by the Department of Agricultural Engineering of the Federal University of Ceará in Brazil, rated power of 6.3 kW is sufficient for most equipment compatible with family farming [23]. Consequently, low-power electric tractors become a viable alternative for small-sized properties, being capable of providing significant improvements and contributing to sustainability through the use of renewable energy sources [24-26]. In this context, family farms also provide great potential for micro-generation [6]. It is also worth mentioning that EVs are much more effective than their ICE-based counterparts and may even be supplied by clean energy sources [27-29]. One of the most important differences in terms of performance is the torque and speed characteristics of the electric motor [14]. Another prominent characteristic of the electric motor is the torque reserve, which is significant to achieve improved traction performance. During a limited time interval, it is possible to generate a maximum torque that exceeds the rated torque by a high factor, i.e. three or more times. In this context, the electric tractor becomes a feasible alternative to contribute to a significant improvement of family farming activities. The propulsion system, which is specially designed for a low-power electric tractor capable of providing driving flexibility and controlling the wheel slip, has not been previously reported in the literature, being this the main contribution of this work. Prominent advantages of the proposed approach are zero carbon emissions, low noise level, high efficiency due to the use of electric motors, and low operation and maintenance costs. 2.1 Electronic architecture The design of the electric tractor prototype represented in Fig. 1 shows the result of a comprehensive validation process involving integrated applications of mechanical, electrical, and agricultural engineering. A configuration featuring two electric motors, where each one of them is dedicated to driving a distinct wheel, has been found to meet improved requirements of robustness and simplicity. Besides, it provides great flexibility in the tractor operation since it allows the driver to control the speed and torque of each wheel independently [30]. Fig. 1Open in figure viewerPowerPoint Simplified architecture of the electric tractor prototype A rear-wheel traction model is adopted in this work, where the tractor is seen as a rigid bodywhose lateral movement is not taken into account. Considering only longitudinalmotion, Fig. 2 shows the forces acting onthe moving electric tractor. Since agricultural tractors often operate at low speeds, the aerodynamicresistance can be neglected as a consequence. The resulting force associatedwith the interaction of the wheel and the soil is called the drawbar force. Theelectric tractor presents a complex wheel–soil interaction, as the dynamic loadon the axles and the wheel model must be included in the following expressions: (1) (2) (3) (4) where m is the tractor mass; is the tractor velocity;Fx is the longitudinal traction force of thewheels; Ft is the drawbar force;Rr is the rolling resistance;Rxf is the front-wheel rollingresistance; Rxr is the rear-wheel rollingresistance; Cr is the rolling coefficient of thetires; Wdf is the front-wheel dynamic load;Wdr is the rear-wheel dynamic load;a is the distance between axles; b is thedistance from the gravity centre to the front axle; and c isthe distance from the gravity centre to the rear axle. Fig. 2Open in figure viewerPowerPoint Acting forces on the tractor The longitudinal wheel slip λ in the model represented in Fig. 2 is given by (5) being the traction wheel speed given by (6) where r and ω are the wheel radius and angular speed, respectively. The electric layout is based on the association of batteries, inverters, and electric motors. A lead–acid battery bank composed of four units is used, whose cost is less than that regarding lithium (Li)-ion counterparts, being this an important issue for the development of a cost-competitive prototype. Each battery is rated at 12 V with coulometric capacity of 200 Ah at 25°C and C/10 rate (10 h discharge rate); discharge current of 20 A; energy capacity of 217 Wh; and cut-off voltage of 10.5 V. Each battery weighs 60.3 kg, being this is an important aspect considering that the bank acts as a counterweight to provide adequate weight distribution. The series connection of the batteries provides the input voltage of 48 V to two inverters. Electric motors and inverters are manufactured by the Brazilian company WEG. Besides, the rated power of each motor is 4.5 kW, as indicated in Fig. 3. Fig. 3Open in figure viewerPowerPoint Parameters of electric motors and inverters Aiming at proper weight distribution, the motors are placed above the rear axle, just below the driver seat, while the batteries are mounted in the front section and directly attached to the chassis. This arrangement results in weight distribution of 40.9–59.1% (front–rear axle). The drive train design comprises of a simple dual chain transmission with a total transmission ratio of 34.6. Thus, considering that the rated rotational speed of the motors is 1715 rpm, the maximum rotational speed of the wheels is 49.5 rpm. The overall dimensions of the proposed prototype are: wheelbase: 1700 mm; overall width: 1400 mm; overall length: 2000 mm; overall height (driver not included): 1100 mm; and ground clearance: 280 mm. 2.2 Propulsion system The propulsion system of EVs consists basically of electric motors, power electronic converters, and ECUs. In this scenario, the study of novel control strategies and energy management technologies is necessary to provide maximum performance and autonomy [31]. For instance, the development of power electronics has led to a significant reduction in costs associated with AC motor drives. Relevant advances in this field include the development of power semiconductors capable of operating at a wide range of currents, voltages, and switching frequencies. Besides, the conception of microcontrollers has also allowed the development of flexible designs, especially when digital signal processors and real-time microcontrollers are employed. The proposed propulsion system of the electric tractor shown in Fig. 4 employs an ECU, which is responsible for drive management. The ECU also controls the inverters by providing them with the control signals necessary to supply power to the electric motors by the required torque and speed. Sensors are used to measure variables, e.g. position, speed, current, voltage, and temperature. Such signals are properly conditioned before they are sent to the processor. The ECU output signals are sent through interface circuits to the analogue inputs (AI1) of both inverters. Fig. 4Open in figure viewerPowerPoint Electric propulsion system architecture The algorithm associated with the control strategies is executed by the microcontroller. AdsPIC30F4013 by Microchip was employed in the implementation of the ECU [32]. The proposed control concept aims tooptimise the performance of the electric tractor during typical manoeuvresassociated with the intended application in rural areas. Fig. 5 shows the proposed drive control system. In this design, the commands sent to the inverters are determined basedon the speed required by the driver through the pedal(Vx), the longitudinal speed(V), the traction wheel speed (VW),the desired slip ratio according to the soil surface(λref), and actual slip ratios measured in eachtraction wheel (λ1 andλ2). Thus, the main resulting functionalitiesare independent drive control of the inverters, speed control, wheel slipcontrol, and monitoring of the current and voltage of the batteries. Fig. 5Open in figure viewerPowerPoint Block diagram of the electric tractor drive controlsystem A supervisory system was also implemented to monitor the variables associated with the inverters.By using an integrated data storage function, it is possible to provideperformance reports, as Elipse SCADA Software was used for this purpose [33]. The communication between thesupervisory system and the inverters occurs through Modbus protocol with remoteterminal unit (RTU) transmission mode. Modbus is an open protocol widely used indistinct devices by several manufacturers. Modbus RTU network employs amaster–slave system for the exchange of messages. Each communication starts withthe master sending a request to a slave, who responds as requested. In bothtelegrams (question and answer), the structure is the same, consisting of anaddress, function code, data, and cyclic redundancy check. The master starts thecommunication by sending a byte to the address associated with the slave. Whensending the reply, the slave also initiates the telegram with its address.Fig. 6 shows the proposed structure forthe supervisory system, which is employed to monitor the inverters. It is alsopossible to insert the ECU in Modbus RTU network or access it independentlythrough the communication protocol RS-232. Fig. 6Open in figure viewerPowerPoint Supervisory system of the electric tractor 3 Experimental results The electric tractor prototype was evaluated to assess its operation and performance properly.The main objective is to analyse the traction characteristic of using with acustomised drive system and the proposed control strategy. To enable a properanalysis of the test results with the electric tractor and establish a faircomparison, the methodology followed in the practical drawbar tests has been basedon document CODE 2 by international organisation OECD [34], which is applicable to perform tests of agriculturaltractors. A conventional tractor using an ICE was also tested for performancebenchmarking. The experimental tests are divided into two sections: analysis of theelectric tractor in a concrete track and tests carried out in the field. 3.1 Tests in a concrete track The drawbar force, wheel speed, wheel slip, and tractor speed are the main parameters that define the electric tractor behaviour. Five traction tests were carried out to verify the operation and performance of the electric tractor in a concrete track without enabling the wheel slip control. The supervisory system was used to record and store data from the load cell, inverters, motor encoders, as well as voltage and current sensors of the batteries. Fig. 7a shows the electric tractor prototype under test, where the location of the supervisory system, batteries, motors, inverters, and ECU can be seen. The 10 kN load cell shown in Fig. 7b was used to measure the traction force on the drawbar of the electric tractor. All tests were developed in a standard concrete track located at the Department of Agricultural Engineering of the Federal University of Ceará, Fortaleza Brazil (geographical data – location/elevation: 3°44′47.7″S 38°34′53.8″W/19 m). Fig. 7Open in figure viewerPowerPoint Structure of the electric tractor (a) Overview, (b) Load cell coupled to the electric tractor Four traction tests (ETT#1–ETT#4) were performed with the same coupled load. One additional test (ETT#5) was developed at maximum load to evaluate the traction forces and determine the maximum traction limit of the electric tractor. A photograph was taken before the tests can be seen in Fig. 8. Each test was carried out over a distance of 50 m. It is also worth mentioning that (7) is used to calculate the average traction force (7) where NFtm is the average net traction force (kN); Fi is the measured instantaneous force in the load cell during the time interval comprising of the actual and last measurements (kN/s); and tp is the time interval required to travel over the length of the test track (s). Fig. 8Open in figure viewerPowerPoint Preparation for the test sessions: the dragged load, in this case, is composed of a two-axle trailer coupled to an ICE tractor model Valtra Series A The available drawbar power is a function of the traction force and speed and is calculated as in the following equation: (8) where Pd is the drawbar power (kW); Ftm is the average traction force (kN); and V is the speed (km/h). The efficiency of the electric tractor is determined by the ratio between the output power at the drawbar and the power provided by the batteries according to the equation (9) where ηet is the efficiency of the electric tractor (%); Pd is the drawbar power (kW); and Pb is the battery bank power (kW). By recording data regarding the monitored variables, it is possible to analyse the tractor performance properly. Table 2 presents the obtained results during five electric tractor test sessions (ETT#). Fig. 9 shows the behaviour of the force on the drawbar during the first four tests, i.e. from ETT#1 to ETT#4. From the graphs in Fig. 9 and the data in Table 2, it is possible to observe that the traction forces in the tests remain balanced. In such tests, the electric tractor average speed remains in the range between 4.74 and 4.76 km/h, thus generating an average traction force between 1766 and 1956 N. The average drawbar power varies accordingly between 2336 and 2573 W. Table 2. Test sheet Electric tractor prototype ETT# 1 2 3 4 5 test run time (50 m), s 38 38 37.9 37.8 58.4 speed, m/s 1.32 1.32 1.32 1.32 0.86 speed, km/h 4.74 4.74 4.75 4.76 3.08 slip, % 12.28 12.28 13.65 13.42 35.79 drawbar power, W 2573 2467 2429 2336 4082 battery power, W 3998 3880 3795 3685 7145 efficiency, % 64.36 63.58 64.02 63.39 57.13 average drawbar force, N 1956 1875 1841 1766 4768 Fig. 9Open in figure viewerPowerPoint Drawbar force during ETT#1–ETT#4 Fig. 10 shows the battery bank performance through current and power graphs in ETT#1–ETT#4. The average battery power varies between 3685 and 3998 W. During test ETT#5 at maximum load condition, the average speed decreased significantly to 3.08 km/h when compared with ETT#1–ETT#4 due to the heavy load. The prototype maintained an average traction force of 4768 N during ETT#5, according to Fig. 11, whereas the average drawbar power was 4082 W. Fig. 12 shows the battery bank performance in ETT #5 through current and power graphs, where the corresponding average battery power was 7145 W. Fig. 10Open in figure viewerPowerPoint Measurements carried out in the battery bank during ETT#1–ETT#4 (a) Current profile, (b) Power profile Fig. 11Open in figure viewerPowerPoint Drawbar force during ETT#5 Fig. 12Open in figure viewerPowerPoint Measurements carried out in the battery bank during ETT#5 (a) Current profile, (b) Power profile The energy flow in the system can be represented by the diagram in Fig. 13. The total energy demand from the battery bank given by Et can be determined from the energy required by the drawbar and losses in the propulsion system according to the following expression: (10) where t0 and tf are the initial and final time instants associated with the tractor operation and P(t) is the instantaneous power. Fig. 13Open in figure viewerPowerPoint Energy flow in the electric tractor The overall system losses are due to the switching losses of the inverters, electromechanical losses of the electric motors, mechanical losses of the transmission system, and friction of the wheels. The overall theoretical efficiency for optimum conditions is calculated based on the individual efficiencies of the tractor components, as shown in Fig. 13 according to the following expression: (11) where the inverter efficiency is , the motor efficiency is , the tran
Referência(s)